Empowering Business Growth Through Plastics Injection Molding
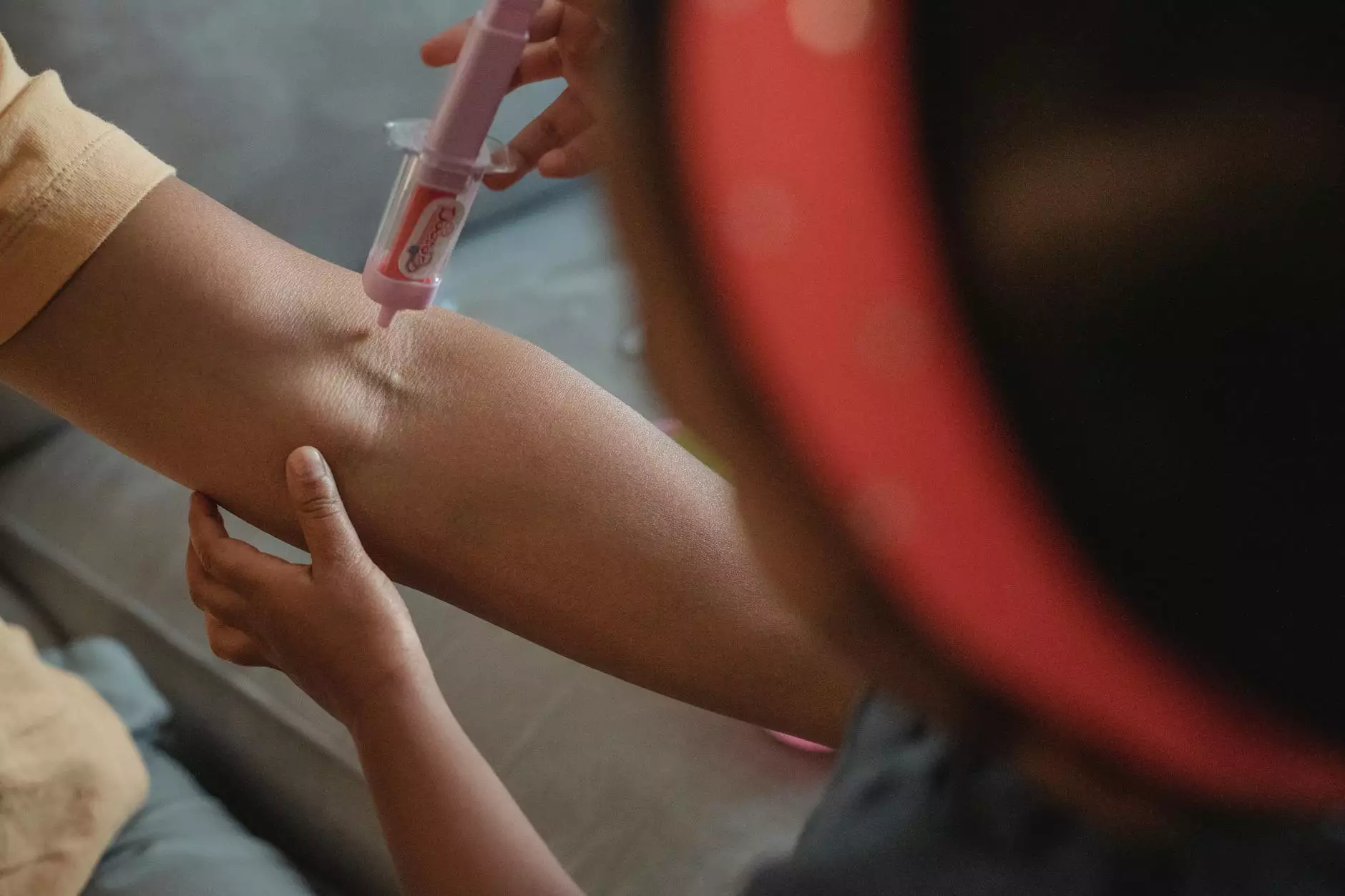
The world of manufacturing has undergone a significant transformation with the advent of modern technologies. Among these innovations, plastics injection molding stands out as a pivotal process that is not only efficient but also essential for various industries, including those involved in metal fabrication. This comprehensive article delves into the intricacies of plastics injection molding and its impactful role in enhancing business operations.
Understanding Plastics Injection Molding
Plastics injection molding is a manufacturing process used to create parts by injecting molten plastic into a mold. It is a highly versatile method capable of producing a wide variety of shapes, sizes, and complexities. This process is notable for its efficiency, durability, and ability to generate consistent results, making it a preferred choice in many sectors.
The Significance of Plastics in Today’s Manufacturing Landscape
In the current era, the importance of plastics cannot be overstated. From consumer products to industrial applications, the demand for plastic components continues to rise. The flexibility, lightweight nature, and corrosion resistance of plastics make them an ideal choice across numerous industries. Key advantages include:
- Cost-Effectiveness: Plastic components are often more affordable to produce than their metal counterparts.
- Design Freedom:Plastics injection molding allows for intricate designs that would be challenging to achieve with traditional manufacturing methods.
- Reduced Waste: The process minimizes material waste since the exact amount of plastic is injected into the mold.
- Rapid Production: Once a mold is created, thousands of identical parts can be produced quickly.
Applications of Plastics Injection Molding in Metal Fabrication
The integration of plastics injection molding in metal fabrication can significantly enhance production capabilities. Here’s how:
1. Prototyping and Design Iteration
In metal fabrication, creating prototypes to test designs can be costly and time-consuming. By utilizing injection-molded plastic prototypes, companies can iterate their designs at a fraction of the cost and time, allowing for faster innovation cycles.
2. Production of Tooling Components
Plastics injection molding can be used to create complex tooling components. This is particularly useful in the metal fabrication industry, where customized tools are needed for specific tasks. Lightweight plastic tools can improve ergonomics and reduce fatigue for workers.
3. Advanced Assemblies and Inserts
In many applications, metal parts require plastic components to hold, insulate, or otherwise interact with other elements. Plastics injection molding facilitates the integration of these plastic parts seamlessly into metal assemblies, enhancing functionality and durability.
The Process of Plastics Injection Molding
The journey of creating a plastic part through this method is intricate and involves several crucial steps:
1. Design and Engineering
This stage involves the creation of a 3D model using CAD (Computer-Aided Design) software, which will dictate the final product’s design.
2. Mold Creation
Once the design is finalized, a mold is created, typically from steel or aluminum. This mold is a critical investment as it will be used to create numerous parts over its operational lifetime.
3. Injection Phase
In this phase, plastic pellets are heated until they melt, after which they are injected into the mold under high pressure. This ensures that the molten plastic fills every nook and cranny of the mold.
4. Cooling and Ejection
After injection, the mold is cooled down, causing the plastic to solidify. The mold is then opened, and the finished part is ejected.
Advantages of Plastics Injection Molding
Plastics injection molding offers numerous advantages that appeal to manufacturers wanting to stay competitive:
- High Efficiency: The speed of production is unparalleled, allowing for high-volume manufacturing.
- Quality Consistency: Each molded part is created with precision, ensuring uniform quality across all units.
- Material Versatility: A wide variety of plastics can be utilized, catering to different needs and specifications.
- Environmental Benefits: Many modern plastics are recyclable, which can contribute to sustainable manufacturing practices.
Challenges and Considerations
While the advantages are numerous, there are challenges associated with plastics injection molding that businesses must navigate:
1. High Initial Costs
Creating molds can be expensive and requires significant upfront investment. However, this cost can be justified with high-volume production runs.
2. Material Limitations
Not all types of plastics may be suitable for injection molding, depending on desired properties such as temperature resistance and toughness.
3. Production Time for Molds
The time taken to design and create molds can delay the start of production. Companies must plan accordingly to avoid bottlenecks in the manufacturing process.
The Future of Plastics Injection Molding
The future of plastics injection molding appears promising, with several trends shaping its evolution:
1. Technological Advancements
Emerging technologies in automation and robotics will likely enhance the efficiency of the injection molding process, further reducing operational costs and increasing output.
2. Sustainable Practices
As the world moves towards sustainability, the industry is seeing a rise in bio-based and biodegradable plastics that can be utilized in injection molding processes.
3. Industry 4.0
The integration of IoT (Internet of Things) and data analytics is set to revolutionize production lines. Smart manufacturing will allow for real-time monitoring and optimization of the injection molding process.
Conclusion
Plastics injection molding is more than just a manufacturing technique; it is a game-changer in the industry landscape. By leveraging its numerous benefits, businesses can significantly improve their production capabilities, reduce costs, and drive innovation. Companies involved in metal fabrication and related fields must consider incorporating this technology into their operations to remain competitive in an ever-evolving market.
In summary, the adoption of plastics injection molding could represent a critical step forward for businesses looking to optimize their manufacturing processes and enhance product offerings. Embracing this technology might not just lead to better products but also foster a more innovative and sustainable approach to manufacturing.
For manufacturers looking for metal fabrication solutions, exploring the integration of plastics injection molding with their existing processes could open new avenues for efficiency and product development.